Serviplast connects its machinery and steps into the 4.0 era
Owned by Serviplast Group whose head office is in Belgium, Serviplast specializes in the expertise and services of plastic injection.
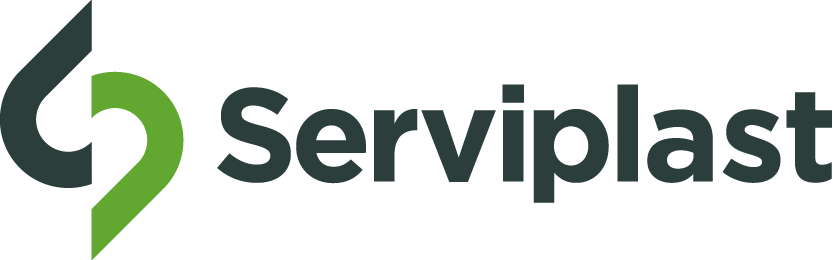
Thanks to our partner Plastiwin (WALLOON BUSINESS CLUSTER FOR PLASTICS INDUSTRY), we meet Serviplast in September 2019 and our collaboration begins then.
After studying their expectations and needs for connectivity, we came to visit the premises of Serviplast in order to discover their machinery.
Back then, a sketch of the layout of their injection molding machine is made in order to subsequently design a view of their factory in isometric (2D).
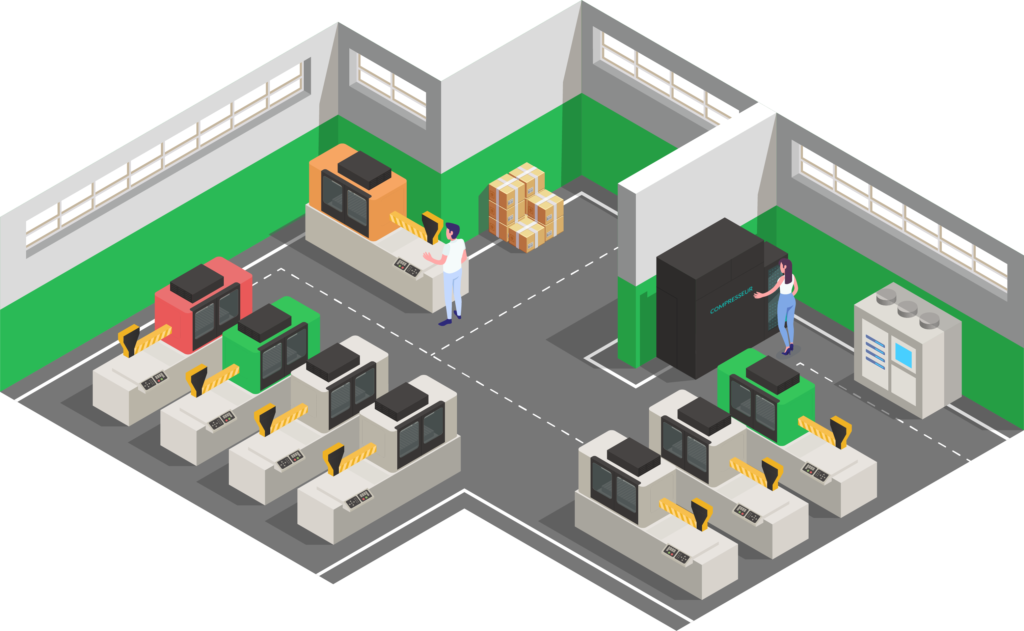
Serviplast then begins its transformation to a new generation of plastics. They start by connecting 11 of their injection molding machines using our kit in order to supervise their production informations and electrical consumption.
They also equipped a compressor and a free cooler with our sensors to measure their energy consumption.
Finally, 6 of our environnemental sensors were installed in different locations of the plant and measure the ambiant temperature and humidity.
Under the supervision of the Ewattch Belgium team, one of Serviplast technicians deployed our solution in their plant. Within a few hours, the entire solution was up and running.
The sensors placed on the Serviplast equipment then began to transmit the collected data to the EwattchCloud platform.
Our team previously configured the Serviplast account in order to facilitate the handling of the platform by users. Then, they personalized their dashboards with valuable informations for our client.
A short training (a few minutes only) was enough for new users to understand the platform and thus, access the new data transmitted from their machinery park:
- Management of production data: cycle time, remaining production, number of parts produced, etc.
- Analysis of energy consumption
- Temperature and humidity of the plant.
- Ability to view data directly in the factory and from their injection molding machine using augmented reality and a QR code installed on the machines.
- And many other features …
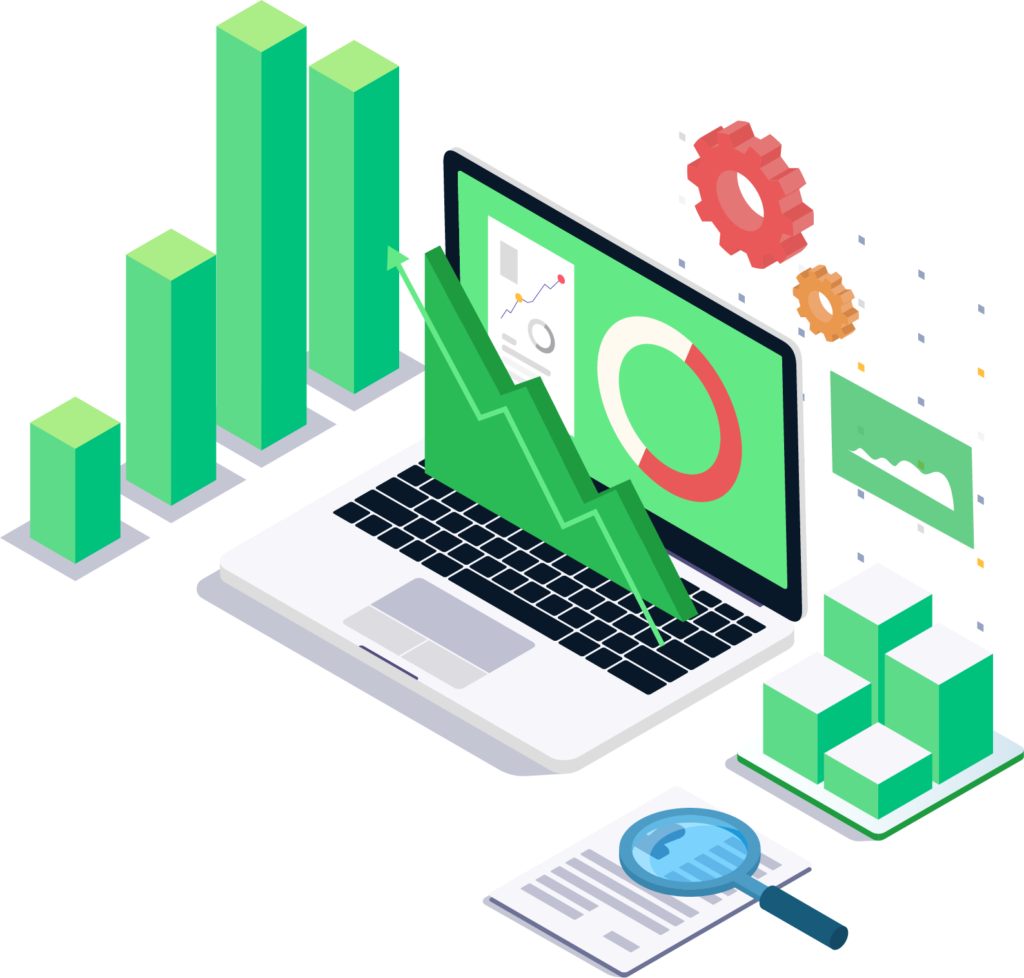
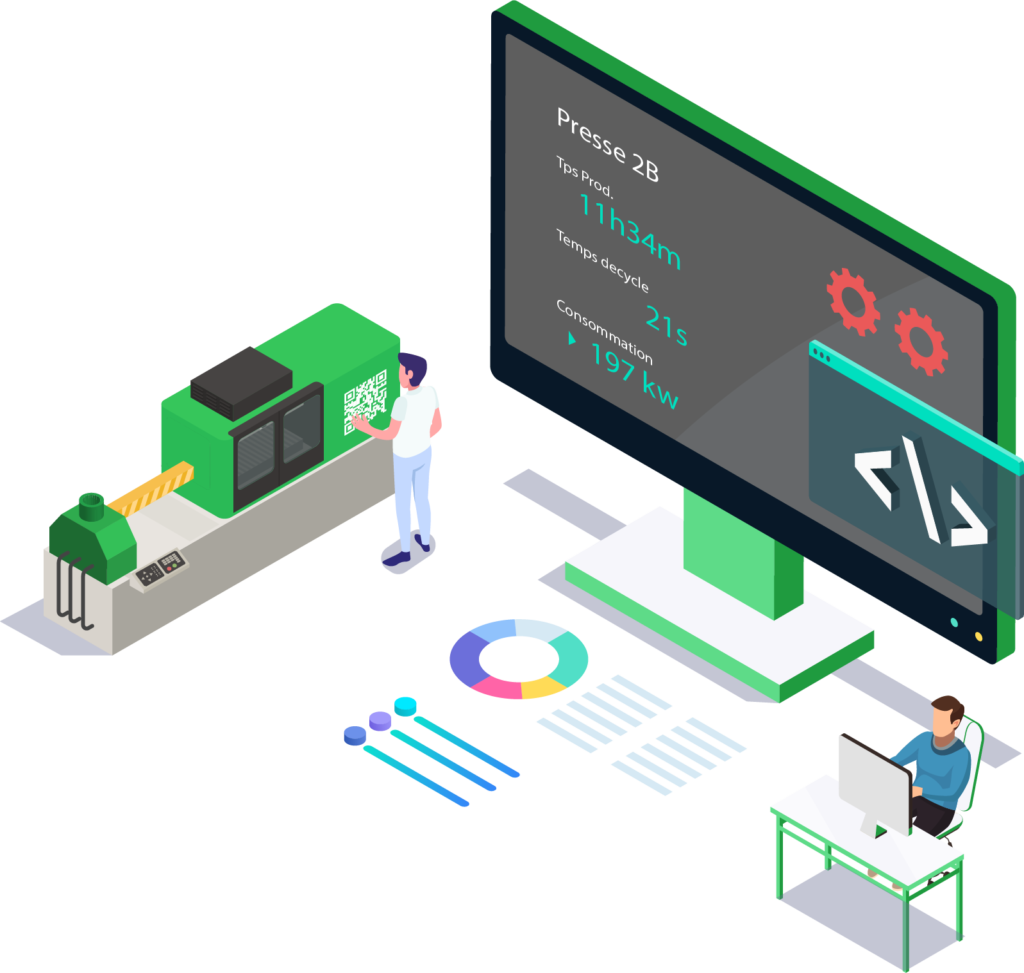
With the installation of the Ewattch Plastics solution, Serviplast can now identify the exact energy consumption of its machinery and dissociate that of its injection molding machine individually.
Thanks to the deployment of this solution, they can now optimize their injection molding machines for production and choose which ones should operate as a priority. They have also started to reduce the overall energy impact of their plant.
Finally, Serviplast has started to determine with greater precision the ROI (Return on investment) of its factory and its machinery.
Moreover, they are considering adaptations in the production and distribution of compressed air and cold production. The addition of a free-cooling system is currently under consideration.
If, you too, have digitalization and connectivity needs within your plastics processing plant, feel free to contact us or call us: +33329577597.
Our plastics experts will gladly help you define your project or answer any questions you may have.